Company Profile
Company Background
Our lighting line now consists of more than 2,000 products in over 280 unique styles. Each light is handcrafted in our factory. Some lights have a more three-dimensional, structured quality about them. They require the most handiwork in that the patina is hand applied, the bark paper is handmade and metal-working is extensive. Other lights are more two-dimensional with almond or amber colored mica setting off the art.
All of our lights are thoughtfully designed for maximum functionality, durability, ease of installation and care. Each light meets or exceeds the standards and requirements of the Underwriters Laboratories, Inc. (UL) for both USA and Canada. Our desire is to provide rustic lodge lighting and cabin lighting products for our customers whose lifestyles reflect their love for the outdoors. We're creating designs that meet the needs of home owners from border-to-border, and mountains to oceans.
Below are some of the steps we follow and the outstanding people (aka "Ranch Hands") we employee located in our Bellingham, Washington Craftory.
Owner/Designer - Curt Roth - Biography
For the past twenty-four years, I have had the pleasure of owning and growing this fantastic decorative lighting business known as Avalanche Ranch Lighting. I am pleased with the products I have designed and this Web site, which contains more than 2,000 lights. I believe this makes us the number one manufacturer and source of rustic lodge lighting in the USA, with more product and more capabilities in this category than any other company. With our lighting design expertise, we work on many custom lighting projects throughout the USA.
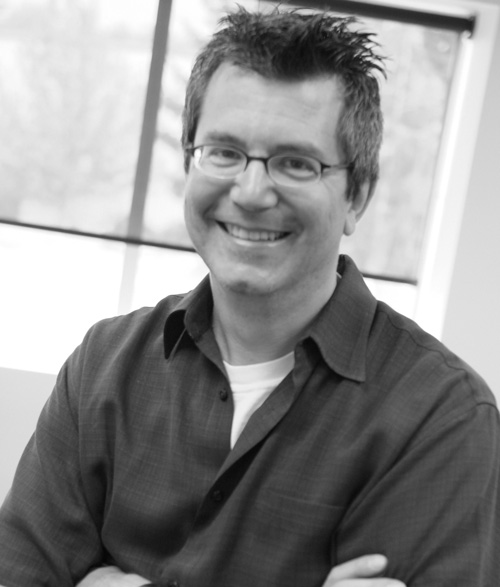
In building this business, I have tried to combine modern production methods with traditional handiwork in an effort to create something unique. I call this business a Craftory, with a focus toward designing and building quality products, keeping our customers happy and developing great employees.
This focus guides my design philosophy as well. While drawing inspiration from the surroundings of the Northwest, I seek to maintain the rustic qualities and northwoods motif of our products, and to create a broad range of designs that look great in a modern, traditional home to a rustic log cabin by the lake (and everywhere in between). I also strive to source the highest quality components and materials, designed to meet the needs of our customers and follow the latest industry technical requirements. As we evolve, you will find more items reflecting a more organic modern lighting direction, with more metallic finishes and some pretty cool designs.
I enjoy my dual role as Owner and Designer and the creative possibilities that these roles hold. I receive the utmost satisfaction from delivering a unique, high-quality light fixture. With an operational team with an average tenure of more than 6 years, we can customize, create new and be a real partner with architects, designers and homeowners in setting the ambiance with lighting, which in my view, is one of the most important elements of creating a comfortable living environment.
Our Production Process
-
Steel Cutting
All of our lights begin their life as a flat piece of steel. Using 16 and 18 gauge mild steel in 4 x 8 foot sheets, the are loaded onto our CNC plasma cutting table for cutting in the various parts for the lights. Typically, only the outside edges are machine cut, as the "inside lines" are cut with a handheld cutting torch. This hand cutting gives each part a unique one of kind look.
-
Steel Forming
All of our steel forming is done by hand. Wall lights have backplates which are bent into shape using a hand brake. Animals, trees and pine cone parts are pounded into shape using hammers and special jigs. We also have hand rollers, small benders, pliers, etc. Handmade, that is what we are all about.
-
Welding
Okay, so the next step is to take the parts cut and formed above and begin the welding process. Our welding team has a long history working at the "Ranch". Through the years, we have created welding jigs and the product knowledge to make a light consistently from one production day to the next. Working from production list and a master template, each light is hand welded into the final product. If the fixture is a custom light, or has modifications from the original design, the welder person refers to detailed shop drawings to make the light.
-
Finishing
Once welded, the light fixture and all of its parts are brought over to the finishing department, ie the powder coating area. Each finish color has its on bin or rack, and one crucial step is to put the light fixture in the right bin, because, at this point, only the welder person knows what color any particular light is to be finished. We use a 7 to 9 step process for finishing our products. Lights are dipped into three liquid tanks for the surface preparation, heat dried, powder is electrostatically sprayed on the light and then baked in a 400 degree oven. Once cooled, the lights are taken to the assembly department. Some colors require multiple steps through the spraying-oven to achieve our special look. Other colors require hand painting of details with a final lacquer coat.
-
Assembly
Lighting parts that are through the finishing department are now ready for assembly. We have multiple work areas set up for assembly, one for each category of light fixtures, such as chandeliers, pendants and wall lights. It takes many months of training for one of our assemblers to master just one of these categories. Full knowledge of the assembly procedures need to be learned: Which sockets to use, how to hand cut the mica or hand bend the mica, how to use the glass making kiln, which hardware pack to use and how to perform the various UL tests required.
-
Boxing and Shipping
Completed lights are placed in plastic bags and are given to the boxing and shipping department. Some orders are master packed together to save on shipping. Other lights require large crates to be built. Care is taken with each light to make sure it arrives at the customers location in one piece.